Metallurgy
Ladle treatment through metallurgical injection Systems
Desiliconization, Dephosphorization, Desulphurization, Triple D, Recarburization, Chemical Heating
Küttner supplies metallurgical treatment stations for hot metal, steel and non-ferrous melts. The technology of choice is injection of solid reagents into the liquid metal. This serves for a variety of different metallurgical tasks, such as Desiliconization, Dephosphorization, Desulphurization or in combination triple D. Depending in the task, suitable reagents are pneumatically injected in the liquid metal by means of one to three pressurized dispensers – called mono-, co- or multi-injection. The latest development is a new process which prepares the optimum blend of reagents at the spot and allows therefore the use of only one dispenser. This direct injection process is ideal to upgrade existing mono-injection plants to the performance of a co- or multi-injection plant.Highly standardized injection units save cost as well as installation and commissioning time and are highly flexible to meet plant requirements.
Küttner has installed more than 100 treatment stands for varying ladle sizes using the deep injection technology in brownfield and greenfield projects from engineering and supply of key components to turnkey solutions.
BOF converter
Efficient bottom stirring for improved Dephosphorization
Bottom stirring is a BOF technology valuable to attain metallurgical benefits such as low oxidation degree of the melt and slag, combined with low Fe-yield losses, low de-oxidation agent and alloying agent consumption. The second important field of benefits from bottom stirring, phosphorous removal calls for using bottom stirring, as the combined technology of top oxygen blowing and inert gas stirring through the bottom, helps significantly to improve bath mixing and thus in shifting the process towards the optimum metallurgical equilibrium conditions.
Küttner installs 8 – 12 tuyeres in the converter bottom to inject inert gases into the steel melt. A valve station automatically provides the optimum amount of gas at an appropriate pressure in every phase of the steelmaking process.
Cost-optimized production of steel grades with carbon contents after end-of-blow of 0.035% or even less is possible with the TBM bottom stirring system. The stirring intensity is adjusted to approach the equilibriums of the refining reactions with carbon, phosphorus and sulfur and allows achievement of minimum gas contents (oxygen, nitrogen and hydrogen) in the steel.
Services
-
Engineering and delivery
-
Conversion of existing systems to state-of-the-art technology
MetInject – Metallurgical Injection Technology (EN)
DownloadDesulphurization Strategies in Oxygen Steelmaking (EN)
DownloadEfficient hot metal pretreatment (EN)
DownloadEntschwefelungstrategien für Blasstahlwerke (DE)
DownloadPretreatment and Refining of Hot Metal (EN)
DownloadLange Konverterreisen durch Slag Splashing und effiziente Nutzung der TBM-Bodenspultechnik (DE)
DownloadExperience with long BOF Campaign Life and TBM Bottom Stirring Technology at Meishan Steel in China (EN)
DownloadUse of Hot Metal With High Phosphorous Content in Combined Blowing BOF Converters (EN)
DownloadReferenzen
The strengths of Küttner
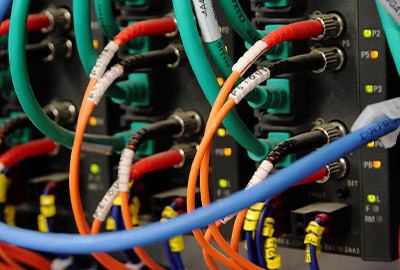
Electric and Automation
New production processes and flexible process technology are placing ever increasing demands on elec…
Read more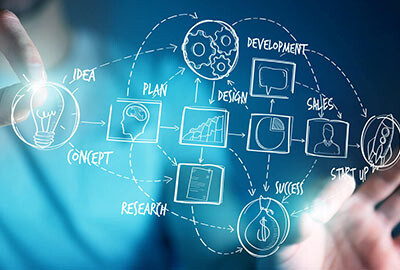
Innovative strength
We make high demands on ourselves first, because this is the only way we remain able to fulfil your …
Read more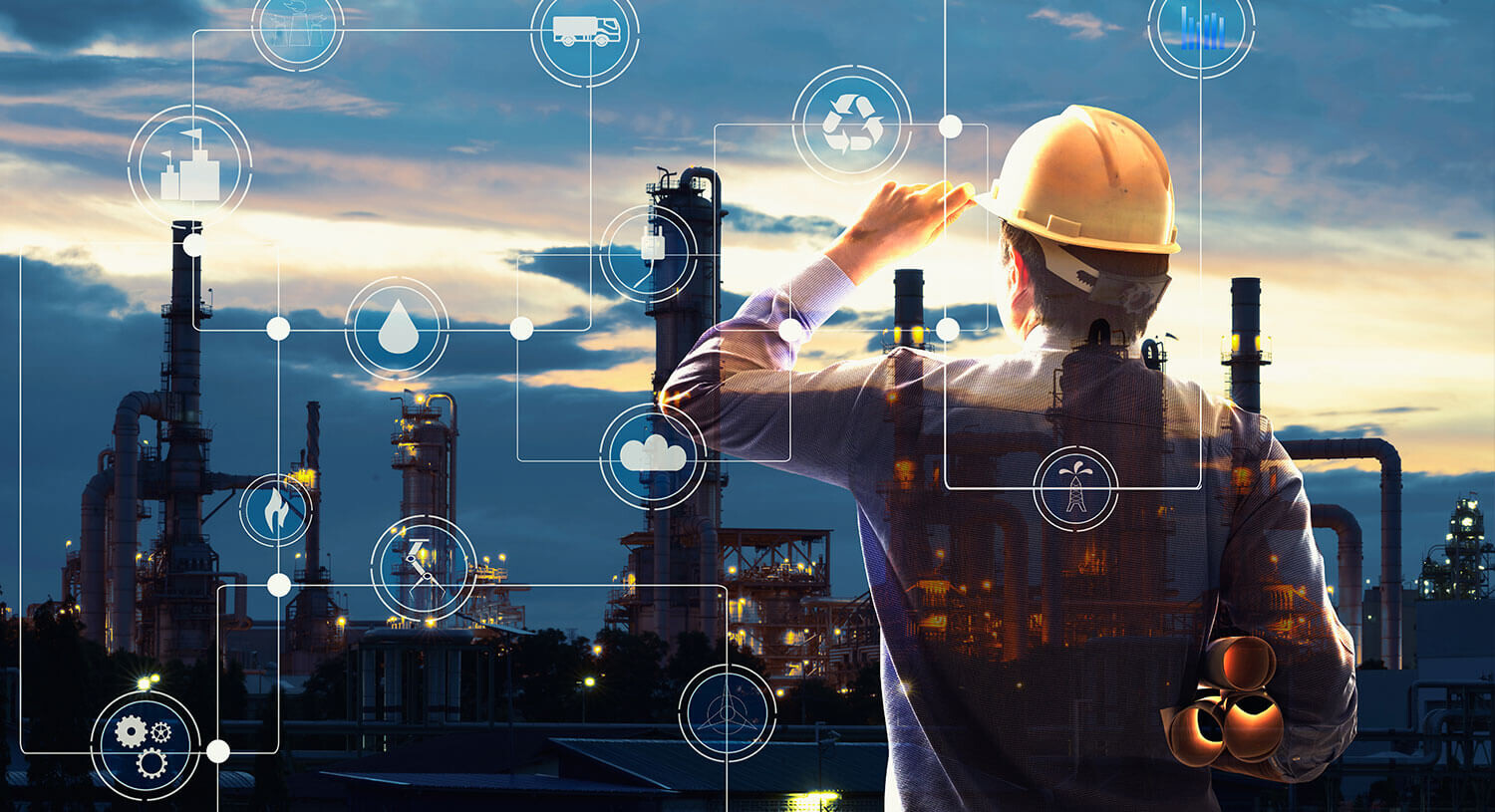
Digital Operations
The fourth industrial revolution is a reality. The real and virtual worlds are moving closer togethe…
Read more