State-of-the-art sand preparation for Friedrich Lohmann
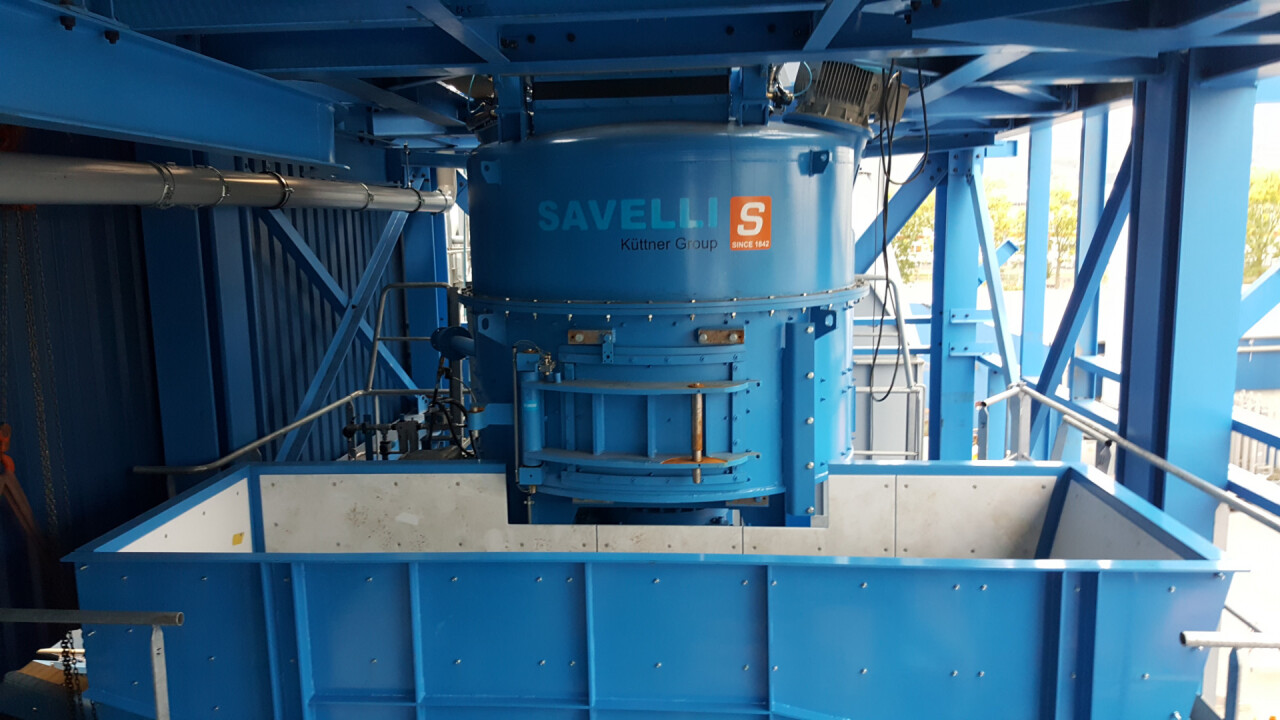
The stainless steel foundry Lohmann in Witten ordered a new sand preparation from Küttner for the energy-efficient and resource-saving production of steel castings. In addition to two automatic molding machines, this central sand preparation also serves single molding machine and a hand molding area, whereby the molding material is manufactured for each consumer according to a separate and automatically selectable recipe which is adapted to the quality requirements of each individual consumer.
Küttner used a Savelli SGMT 1500 mixer as the core component of the sand preparation with the AQUATEST moisture measurement system and the SANDCONTROL automatic compactability and compression strength tester.
The molding material control concept used represents a combination of online control with the help of tests and predictive tools.
The aim of the sand preparation control is to achieve a molding sand as constant as possible in composition and quality. To achieve a stable compactability, the water is added in two steps: primary water, calculated from the difference between the nominal water requirement and used sand, and correction water, calculated from the difference between the target and actual compactability on the basis of an online compactibility test. At the end of the mixing cycle, a second material test is carried out as a proof of quality and for optimization of the correction factors. The bentonite is added intelligently based on the previous batches. By evaluating the online compressive strength measurement based on an moisture-compactability active-clay control diagram, an online correction of the molding compound takes place with respect to a set compressive strength.
In addition to the results of the on-line material testing, a material balance with consumption and used sand data is created and evaluated for quality control. As part of the Industrie 4.0 approach, complex information are used here:
- All consumption and production data and machine parameters recorded in seconds and maintained by a special Industial Information Management Systems "iIM". The iIM is used by the Küttner for the first in a sand processing;
- All results of the Online Formstoffprüfung, z. Also, to maintain and update the Humidity Compensability Active Tone Control Chart yours;
- Landfill quantities - excess sand, oversize / tuber discharge, filter dust;
- Model-related production data, such as liquid iron per box, core sand content, cast-sand ratio, etc.
As a result of this balances, the specific consumptions of additives are determined.
The iIM generates trend analyzes from the recorded material data and also enables comparison and manual intervention.
The application of the Industry 4.0 methods by the iIM shows very good results. As a result, mold material accounting is increasingly being taken over by data-driven models. These models capture all relevant data and independently optimize the corresponding correction factors, such as the online controlled quality parameters compactability and compressive strength, thereby achieving a very stable quality.
The Küttner Life Cycle App was also used for the first time in the foundry industry for this project. The app supported commissioning by having already stored all necessary function and signal tests in advance, as well as the complete machine documentation. By checking the respective tests, the project manager is always informed about the current status. In addition, this app supports the maintenance.